Products
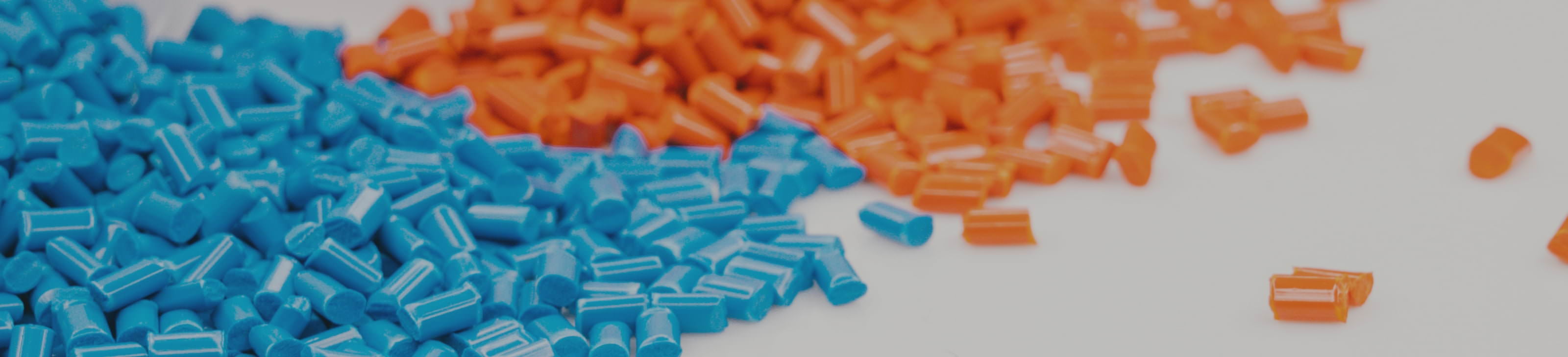
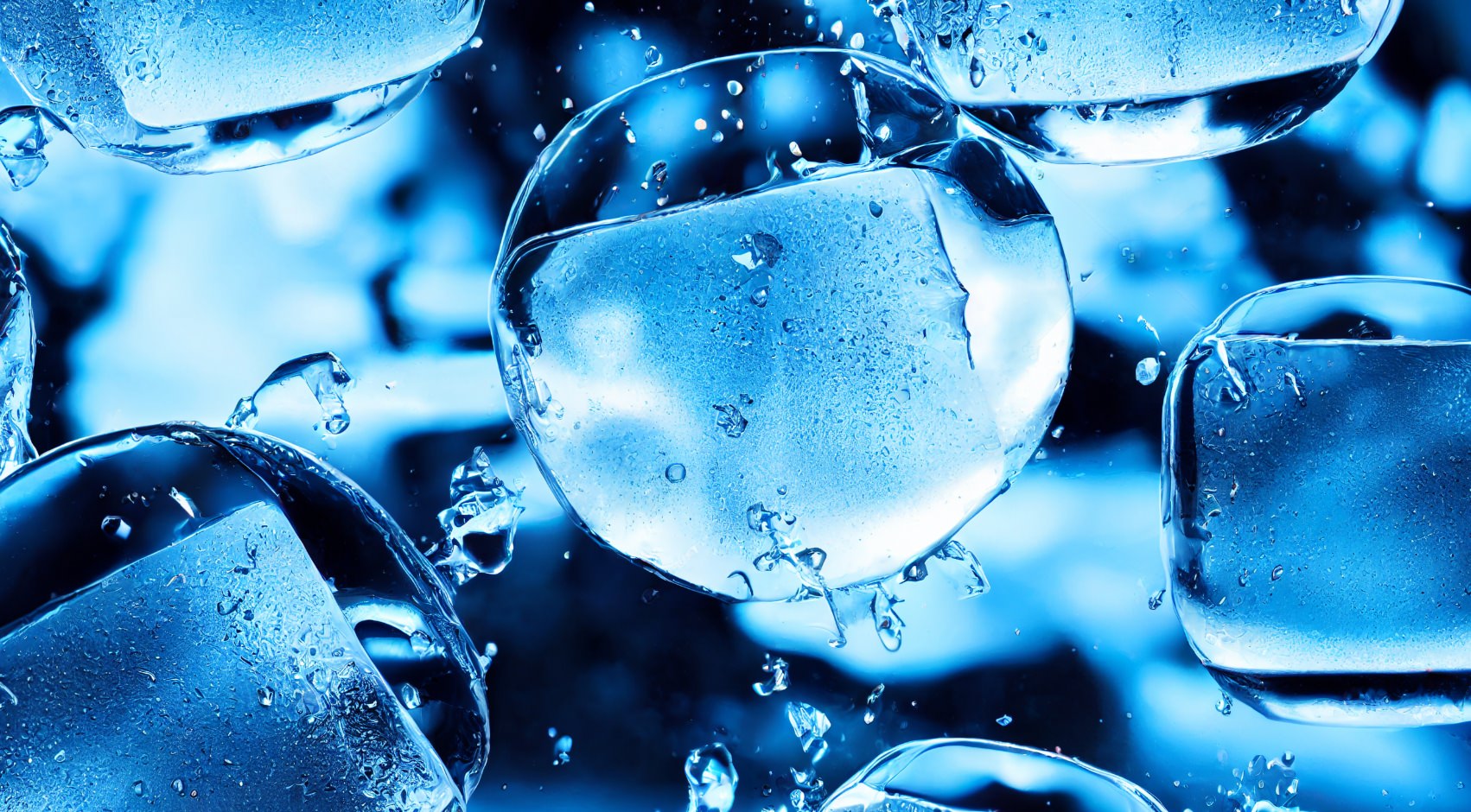
PBT is a polyester resin obtained by polycondensation of terephthalic acid (TPA) and 1,4-butanediol (1,4-BG).
It has excellent electrical insulation performance, good chemical resistance, moldability, colorability, etc.
Taking advantage of these characteristics, it has been widely used as a material for automotive, E&E, and high-performance film applications.
Special features
Technical Datasheet
Advice on using Polybutylene terephthalate resin (PBT resin)
About the physical properties of PBT resin
Polybutylene terephthalate (PBT) resin is a crystalline resin which is produced through polycondensation of terephthalic acid and 1,4-butanediol (or 1,4-dihydroxybutane) as basic raw materials and has the following macromolecular structure.

Since PBT resin has well-balanced properties (mechanical/thermal/electrical properties, dimensional stability, resistance to chemicals excluding strong alkali, molded surface gloss, colorability, and enable to create flame retardant grades, etc.), crystallizes fast, and has high molten flowability, it can be injection-molded in high cycles. On the other hand, it has also disadvantages in that it has low hydrothermal (hydrolysis) resistance and tendency to generate dent (a phenomenon of shrinkage in the mold) and warpage due to crystallization. PBT resin with the characteristics as explained above is used for electric and electronic components as well as automotive parts.
About the molding of PBT resin
Polybutylene terephthalate (PBT) resin is used not only in injection molding applications but also extrusion molding such as food and fluid packaging, lamination with paper or metal, shrink film, protective tubing, and decorative steel plates, etc. by being processed into films and tubes, because it has superior resistance to thermal distortion and chemicals, smell barrier properties, pinhole resistance, food hygienic properties, and formability (e.g., deep drawing).
About PBT resin drying conditions
It is absolutely necessary to dry Polybutylene terephthalate (PBT) resin because it causes a reduction in physical properties due to hydrolysis when it is molded in the water absorption state. However, it causes heat degradation when it is excessively dried. Therefore, it is important to control the water content appropriately to keep the water absorption rate at 0.03% or lower. The hot air drying conditions recommended to make the water absorption at 0.03% or lower are 4 – 6 hours at 140℃ and 5 – 8 hours at 120℃. In addition, it is recommended to mold PBT resin within 30 minutes after dried because it absorbs moisture when left in the atmosphere.
[Explanation] About the characteristics of crystalline and amorphous resins
(1) Macromolecule crystallization
Crystallization of macromolecule (in this document, linear polymer molecule is set forth as a premise for explaining the principle) refers to a phenomenon in which parts of chainlike polymeric molecule gather together to make up flux which are partially arranged in one direction under certain given conditions, for example, under the cooling conditions in the molten state during injection molding or the concentrating conditions in the solution state (Refer to Figure 2), although it refers to a phenomenon in which small molecules and ions are arranged systematically to make up a crystal in the case of molecular crystals (Example: sugar) and ionic crystals (Example: salt) (Refer to Figure 1). In addition, when macromolecules crystalize, amorphous regions with varying molecular conformation other than such crystalline region normally exist together.
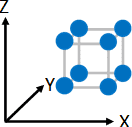
blue represents molecules or ions and grey represents crystal lattices (hypothetical concept).
The same crystal lattices continue systematically in the directions of X, Y, and Z axes.
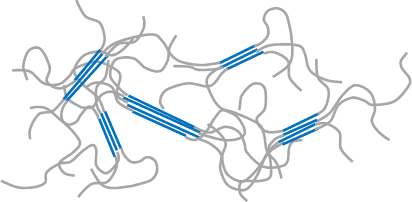
blue represents crystalline regions and grey represents amorphous regions. In the crystalline regions, macromolecular chains form fluxes in the same direction.
In the amorphous regions, macromolecular chains locate indeterminately.
The both crystallizations have a common feature that molecules, ions and polymeric repeating units (monomer units) seek to employ the most stable conformation thermodynamically, using intermolecular forces or ionic binding as driving forces. However, the macromolecule case is essentially different from the ones of low molecular or ionic crystals because of the less freedom of macromolecular mobility than monomers (low molecules) before polymerization; i.e., monomer units are bundled each other within a polymeric chain. This reduction of molecular mobility unique to macromolecules is the cause of remaining amorphous regions. Furthermore, the proportion of crystalline region (“crystallinity”) and the sizes of respective crystalline regions (“crystal size or crystallite size”) are largely dependent on the molding conditions.
Macromolecular chains are basically amorphous when in the molten or solution state, but they crystallize as cooled or concentrated because the effect of intermolecular force (attractive force) becomes evident. However, macromolecules have one more characteristic that their viscosity increases significantly as cooled or concentrated in the molten or solution states, respectively, compared to low molecule systems. Due to this viscosity increase effect, it actually happens that macromolecules become solidified before they crystallize well. Therefore, in general, the crystallinity can be increased by taking a longer time for macromolecular chains to relocate them through slow cooling or slow concentration. It can be understood that so-called amorphous resins such as polycarbonate resin (PC resin) and polyphenylene ether resin (PPE resin) tend to solidify in an amorphous state in the molding process, because they crystallize slowly.
(2) The properties of the crystalline region of macromolecules
Since the crystalline region has a dense structure based on strong intermolecular force, they generally show a higher thermal softening temperature and elastic modulus as well as lower coefficient of linear thermal expansion (CLTE) and water absorption rate (that is, a reduction in dimension change due to temperature and humidity) than those of the amorphous region. Of these, thermal softening temperature roughly corresponds to, in the amorphous region, the glass transition temperature (Tg) which correlates with the rigidity of monomer unit structure (the lowness of mobility or flexibility of molecular structure); but in the crystal region corresponds to the melting point (hereinafter quote as “Tm”) which is higher than Tg.
Therefore, in resin molded articles, the increase of the crystallinity moves above physical properties generally to the preferred direction. However, since the crystalline regions dispersed in the amorphous region function as a stress concentration point induced by external force due to a difference in elastic modulus, the toughness of resin molded articles generally decreases as the crystallinity increases and moves in the direction of embrittlement. If the crystallinity is the same, toughness can be improved by reducing the crystalline size.
(3) The properties of the amorphous regions of macromolecules
The amorphous region in resin molded articles functions as a matrix (continuous phase) containing the crystalline regions (hard and difficult to be thermally-softened) as “fillers” (reinforcing materials to be filled). Although the thermal properties of the amorphous region are dominated by the aforementioned Tg, for the mechanical properties it is important to understand mechanism of the amorphous region exhibiting toughness (durability).
At temperatures lower than Tg, the amorphous region subjected to external force (e.g., tensile, flexural, compressive and torsional stresses, as well as gravity force causing self-weight deformation) causes reversible (elastic) deformation first. This phenomenon is relatively small deformation which can be restored by eliminating the external force, and can also be observed in hard and brittle materials such as inorganic glass. However, the toughness of the amorphous region, in terms of a molecular discussion, depends on how far irreversible (plastic) deformation is allowed after the elastic deformation limit. The nature of the plastic deformation is a process of viscous flow, that is, a process in which macromolecular chains tangled with each other dissipate the energy of external force as heat by moving irreversibly to change their arrangement (conformation) gradually and the entire material deforms while bearing breakage.
A trigger which leads plastic deformation to breakage is occurrence of micro-crack (cleavage) and micro-void. Assuming an ideal amorphous region, that is a case where stress concentration factors such as foreign matter and inhomogeneous structure (e.g., crystalline regions, fluctuation of density in amorphous) do not exist, micro-cracks/voids are considered to be caused by (1) macromolecular chain ends, (2) unbinding of macromolecular chain entanglements, and (3) breakage of macromolecular chains, which could be the cause of very tiny voids in the molecular dimension can be generated in the macroscopic deformation. Among these three factors, (1) and (2) are reduced as the molecular weight increases, because the smaller the number of molecular ends per unit weight becomes and the more difficult the entangled chains become unbound, the larger (the longer) the molecular weight becomes (It can be estimated from an example that the longer the boiled noodles are, the more difficult to unbind the entanglements involved in the entire noodle). That is, larger molecular weight is better for toughness.
Concerning the above (3) Breakage of macromolecular chains which is also associated with the perspective of entanglement as described in the above (2), the hardness of the macromolecular chain (the rigidity of monomer unit structure) is one of the factors. That is, if macromolecular chains are flexible, they can follow the entire deformation without eliminating the molecular entanglements. However, if they are rigid, they cannot follow the deformation due to low mobility and stress is concentrated in the entangled points. As a result, it is considered that breakage of macromolecular chains tends to occur. It can be said that the rigidity of macromolecular chains is the cause of complicated behaviors which contradict each other in a practical way. That is, the higher rigidity increases the elastic modulus of amorphous regions and also increases the aforementioned Tg (increases the thermal softening temperature) but reduces melt flowability (increases the molten viscosity to deteriorate the moldability) as thermal properties. On the other hand, if the molecular weight is decreased to increase the melt flowability, the toughness is reduced as described above.
(4) Crystalline and amorphous resins
Basically, linear polymer molecules have the capability to crystallize under certain cooling or concentration conditions. However, “crystalline resins” generally refer to resins which undergo crystallization so that practically preferred physical property balance is shown under common injection or extrusion molding conditions. On the other hand, “amorphous resins” refer to resins which almost do not crystallize under such common molding conditions.
Engineering plastic materials as “crystalline resin” including Polyamide (PA) resin, Polyacetal (or Polyoxymethylene, POM) resin, Polybutylene terephthalate (PBT) resin, Polyethylene terephthalate (PET) resin, and Polyphenylenesulfide (PPS) resins, etc. are characterized by superior molten flowability and chemical resistance, as well as a profound reinforcing effect (an effect of improving elastic modulus, strength, and heat resistance) by compounding fillers such as glass fiber.
The ones as “amorphous resin” including Polycarbonate (PC) resin, modified Polyphenylene ether (m-PPE) resin, and Polyalylate (PAR) resin, etc. are characterized by transparency, anisotropy, and small molding shrinkage.